In his research on freshwater systems in the DC/Virginia area, George Mason University College of Science professor R. Christian Jones was spending much of his time hauling boats. Too much, he thought.
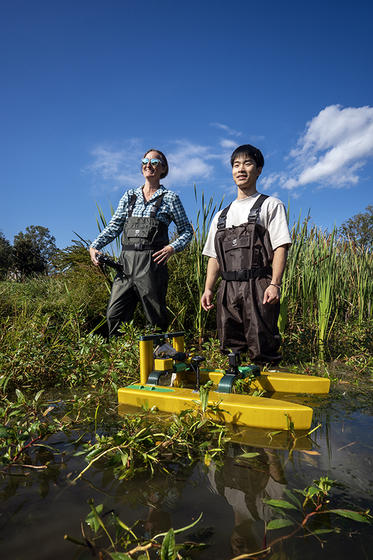
“In order to take a sample from a pond,” he said, “I would need to haul a boat in, put the equipment in, launch it, and then bring it all back. It would add at least an hour and required the body of water to have an access point for a boat.”
As the director of Mason’s Potomac Environmental Research and Education Center (PEREC), Jones knew of a colleague who also works at the Potomac Science Center (PSC) where PEREC is housed, and who could help with this conundrum. He approached College of Engineering and Computing professor Leigh McCue and undergraduate student Ze Li with an idea: a machine that could go out on the pond, skim for plankton samples and collect water samples, and return to shore—all while the researcher remains on land.
This project is part of a larger grant from the National Science Foundation for Persistent and Accessible Maritime Monitoring (PAMM), of which McCue is the lead investigator. The multiyear grant—awarded in 2022 for more than $500,000—focuses on increasing educational, research, and robotics operations and development for students ranging from sixth grade to graduate level, in order to improve the applications of and expanded the use of unmanned marine vehicles. It also includes making such vehicles more accessible for individuals with motion limitations, which in turn can increase accessibility for all researchers.
“Researchers around the globe are utilizing robotics to conduct maritime research, which is an increasingly critical field of study,” explained McCue. “Through this grant, we’re developing more affordable maritime research tools to improve access for great science, whether citizen science or research-grade science. This project fit nicely into that mission.”
The autonomous surface water device created by Li this summer was built from scratch using CAD modeling and 3D printed materials. Li’s experience working with robotics through extracurriculars like his job with Starship Technologies—the company that manages the famous food robots seen rolling around campus—and the Mason Innovation Exchange’s (MIX) 3D printing training helped him navigate the challenges of creating this brand-new machine.
"We thought it was more beneficial to create something new by developing our design around an open-source hull model," Li said. “There’s more opportunity for us to iterate on the prototype.”
The team hopes to continue to improve the machine’s design, now that it’s being field-tested by Jones: improved autonomous capabilities and controls are both on the short list of potential improvements. Li also sees a potential for expanded testing of such data points as water temperature, turbidity, and salinity.
Jones predicts that this machine will be a boon for both access and efficiency. “The number of accessible ponds will increase dramatically with this, and we’ll be able to sample up to eight in a day instead of just one or two,” Jones said.
The machine will also allow for more immediate responses to sudden, unpredictable, and time-sensitive events, like taking samples immediately after storms. Jones even sees possible uses for this machine to take samples during major pollution events, keeping the researchers safe from exposure to harmful chemicals while still acquiring necessary data.
Jones emphasized that this project was made possible by the collaboration between the two colleges. “At a place like PSC where we’re all working together, seeing each other's labs and hearing about research, this sort of collaboration comes naturally,” he said. “It’s a beautiful opportunity for us all to become better researchers and do better science.”
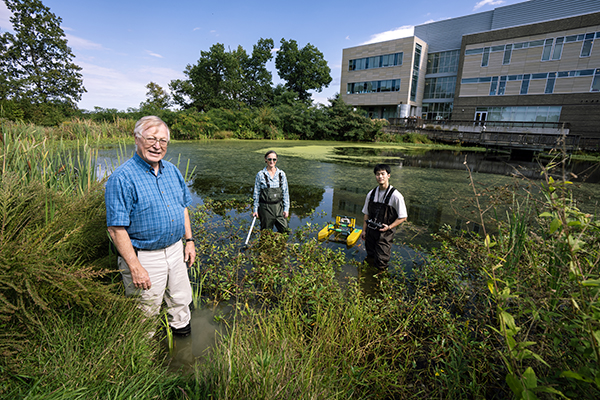
In This Story
Related News
- May 24, 2024
- April 16, 2024
- October 18, 2023
- January 3, 2023
- July 20, 2021
This content appears in the Spring 2024 print edition of the Mason Spirit Magazine with the title "Meet the new Mason-built surface water robot."